Should Costing for Home Appliances
Cost engineering for refrigerators, washing machines, air conditioners, and kitchen appliances — executed by ASI Engineering using xcPEP.
Home appliances are built using a combination of compressors, foamed cabinets, BLDC motors, control PCBs, and injection moulded plastics. These systems span electrical, thermal, and mechanical domains and often interact, where a change in one part can shift cost across multiple operations or suppliers. Accurate should costing is necessary to reflect this structure and capture the true cost behavior of each component.
Cost control in these platforms is made difficult by multi-material assemblies, tooling-intensive parts, and regional sourcing variation. Standard costing tools rarely account for actual production methods or the process-level dependencies seen in appliance programs.
ASI Engineering executes should costing for home appliance products. Each part is modelled based on its actual manufacturing method, using inputs from teardown, drawings, or CAD. Process flows are defined using real production logic, and region-specific input rates are applied from our xcPROC database. All cost models are executed and delivered inside xcPEP for internal use across sourcing, design, and benchmarking teams.
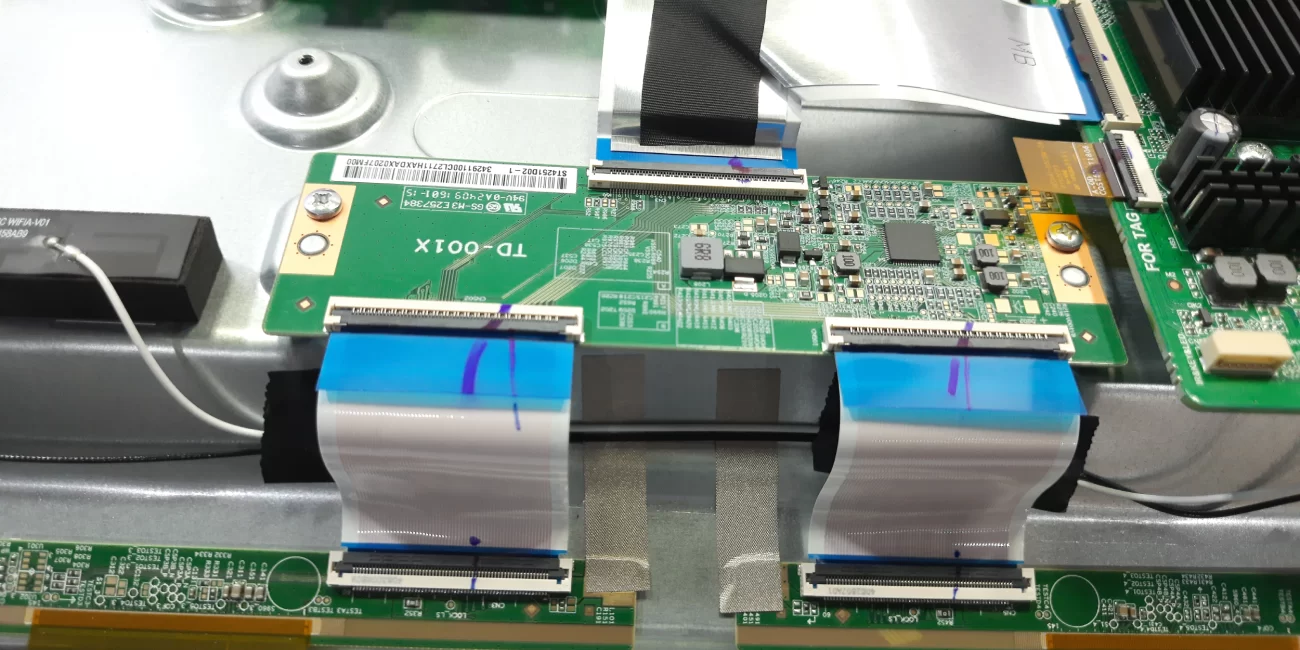
Why consultants, Excel models, and legacy tools fail in
Home Appliances Should Costing
Should costing in appliances like washing machines, mixers, and microwaves is challenging because small changes affect multiple systems. In a washing machine, altering the tub size or spin speed changes motor winding, PCB logic, and bracket design. A different drum material can impact moulding time, assembly steps, and balance weight selection. These interactions are not visible in a standard BOM.
Most teams still use Excel or static cost templates. These tools do not capture real manufacturing steps and often miss operations like vibration welding of detergent trays, over moulding of harness joints, or slot fill variation in BLDC motors. Consultants and benchmark providers typically apply average rates or flat percentages without tracing how the part is actually made.
ASI Engineering builds detailed cost models for every system in a home appliance. Our team captures inputs from teardown, drawings, or CAD, then maps the manufacturing steps as they happen on the shop floor — including forming, winding, moulding, assembly, and testing. Region specific rates are applied using data from our xcPROC database. Each part is modelled based on how it is actually made, and the costing is delivered inside xcPEP for practical use by sourcing, design, and cost control teams.
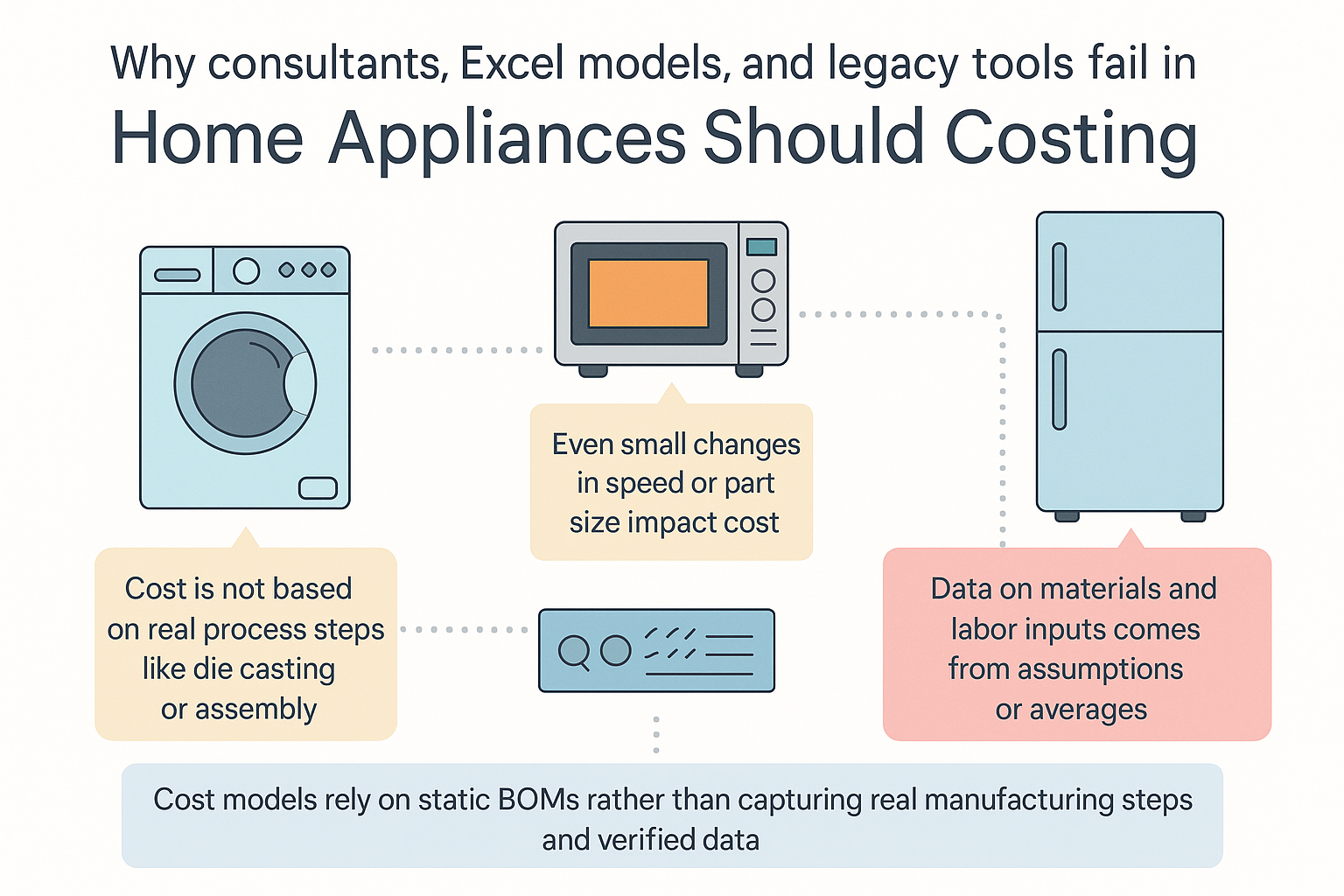
ASI Engineering captures how home appliances are actually built — mapping every manufacturing step so that each cost model reflects real production, not just part names and material types.
Design changes affect multiple systems
In home appliances, small design changes often impact more than one system. Increasing drum size or motor RPM in a washing machine can change the control PCB, bracket layout, drive belt, and even vibration isolation. These dependencies are rarely captured in standard costing models. Excel sheets only adjust part prices, without re-evaluating process flow or cycle time. ASI Engineering traces these impacts by re-modelling each part with updated specs, then re-costing inside xcPEP using real manufacturing steps, volumes, and rates.
Bought-out parts have no internal visibility
Compressors, motor modules, and PCB assemblies are usually procured as complete units. Most tools treat them as single-line items, with no insight into what drives the cost. Cost consultants apply top-down estimates, and benchmarks rely on external averages. ASI Engineering tears down these assemblies, identifies internal components, maps manufacturing operations, and builds a structured cost model in xcPEP. This gives sourcing teams a part-wise view of how the system is built and where cost comes from.
Tooling defines part cost in plastics and foaming
Tubs, trays, and structural enclosures are produced using tooling-intensive methods like injection moulding or thermoforming. Their cost depends on tool design, cycle time, cooling rate, and number of cavities — not just material. Traditional tools apply per-kg costing or ignore tool amortisation entirely. ASI Engineering models the tooling layout and maps actual process time based on geometry and resin type. These parameters are built into each xcPEP model and update automatically across variants.
Mechanical and electrical systems are costed in isolation
A change in motor performance may affect the PCB, sensor wiring, frame design, and assembly test time. In most costing tools, these are treated as separate components with no cost linkage. This disconnects leads to inaccurate targets and missed trade-offs. ASI Engineering connects all relevant subassemblies inside xcPEP. When a spec changes, the model updates connected steps like motor winding, PCB placement, or bracket welding, ensuring the full impact is visible.
No reference cost for local sourcing decisions
When switching to a local supplier for motors, harnesses, or compressors, teams often have no baseline for what the part should cost. Most estimates use region-wide averages or historical quotes, which miss supplier-level differences in process and scale. ASI Engineering builds first-principles cost models using real production logic, applies region-specific inputs from xcPROC, and delivers the output in xcPEP. This gives internal teams a grounded reference when validating or negotiating supplier quotes.
Home Appliance Should Costing in xcPEP
Part-level costing with actual manufacturing steps, input rates, and process-specific overheads.
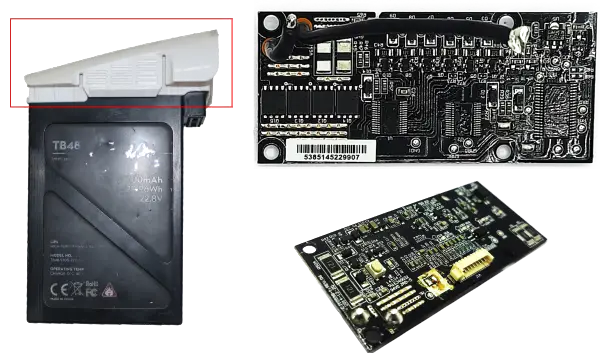
How ASI Engineering Executes Home Appliance Costing in
xcPEP
xcPEP is designed for detailed cost modelling of home appliances, where parts are large, built from multiple materials, and must meet tight cost and energy targets. xcPEP uses data from teardown, 2D drawings, or CAD models to create cost models based on real production steps like injection moulding, sheet metal forming, PU foaming, painting, and PCB assembly. Each step reflects actual manufacturing to ensure both mechanical and electrical parts are costed accurately.
ASI Engineering breaks down key modules like compressors, motors, tubs, harnesses, PCBs, and foamed cabinets. Each part is mapped with actual factory processes—using real cycle times, scrap rates, labour effort, and supplier inputs via xcPROC—capturing tooling, material usage, and overheads precisely.
Whether it's a refrigerator, washing machine, or split AC, xcPEP gives teams clear, structured cost models at both part and system levels. This helps in setting target costs, comparing supplier quotes, and finding cost-saving ideas that are backed by real manufacturing data.
Comprehensive, Part-Level Costing for Home Appliances
Cycle times, scrap rates, machine loads, and regional labour costs are sourced from xcPROC and applied in xcPEP, resulting in a complete and transparent cost model that mirrors real production. This gives sourcing and design teams the clarity to set targets, validate quotes, and drive informed cost-reduction initiatives.
In depth Costing of Wiring Harnesses and Connectors
In depth Costing of Plastic and Sheet Metal Parts
In Depth Costing of PCBs and Electronic Boards
ASI Engineering performs detailed cost modelling for inverter boards, control PCBs, display units, and other electronic assemblies. Each board is analysed for layer count, component density, soldering type, and testing method. Real data from xcPROC is used to calculate machine time, labour, and material cost, giving an accurate cost structure for each board
Accurate Inputs for Cost Modelling
ASI Engineering uses a comprehensive set of verified inputs when building part-level cost models for home appliances. This includes machine hour rates, labour hour rates, raw material prices, currency conversion, and detailed process operations—all tailored to the specific region and manufacturing method. All input data is sourced from xcPROC, ensuring that each cost estimate reflects actual factory conditions, material costs, and production logic with no generic assumptions.
Scenario Costing for Design and Supplier Changes
ASI Engineering uses xcPEP to simulate the cost impact of design changes, alternate materials, or new sourcing decisions. Multiple scenarios can be created, saved, and compared to support clear decision-making.
xcPEP
xcPROC
Cost Models for Home Appliances
Comprehensive, process-wise costing built inside xcPEP by ASI Engineering.
ASI Engineering builds detailed cost models for every manufacturing process used in home appliances, from injection moulding and welding to foaming, PCB assembly, and surface finishing. Each process is modelled based on actual production logic and region-specific input rates using xcPROC. These cost models are structured inside xcPEP and can be applied directly to part level costing across appliance systems.
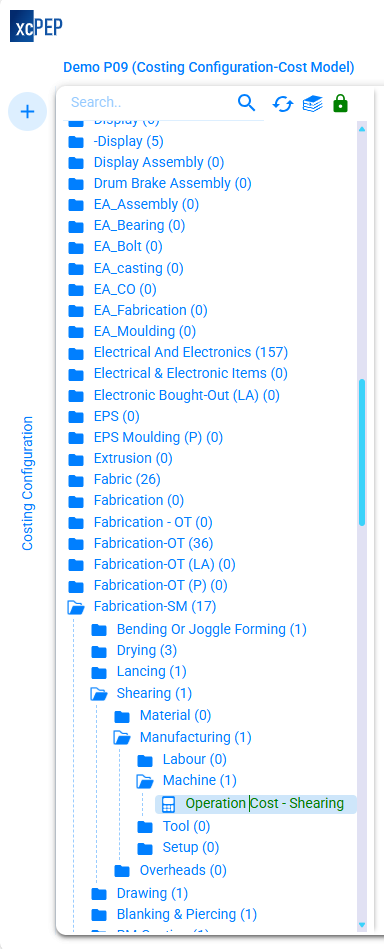
Plastic Moulding
Injection Moulding
- Hot Runner Moulding
- Cold Runner Moulding
- Multi-Cavity Moulding
- 2K / Dual Shot Moulding
Insert & Overmoulding
- Insert Moulding
- Vertical Insert Moulding
- Soft Overmoulding
- Multi-Material Overmoulding
Gas-Assisted Moulding
- Internal Gas Injection
- Short Shot Moulding
- Hollow Section Moulding
Other Moulding Processes
- Blow Moulding
- Rotational Moulding
- Thermoforming
- Vacuum Forming
Welding & Joining
Spot & Resistance Welding
- Spot Welding
- Projection Welding
- Seam Welding
- Cross Wire Welding
Arc & MIG Welding
- Manual Arc Welding
- MIG Welding
- TIG Welding
- Continuous Seam Welding
Ultrasonic & Plastic Welding
- Ultrasonic Spot Welding
- Ultrasonic Line Welding
- Vibration Welding
- Hot Plate Welding
Joining Techniques
- Riveting
- Clinching
- Adhesive Bonding
- Screw Fastening
Surface Finishing
Painting & Coating
- Powder Coating
- Electrostatic Spray Painting
- Epoxy Coating
- Liquid Enamel Coating
Pre-Treatment
- Degreasing
- Phosphating
- Passivation
- Water Rinsing
Metal Plating
- Nickel Plating
- Chrome Plating
- Zinc Plating
- Electroplating
Surface Finishing
- Buffing
- Polishing
- Sanding
- Shot Blasting
Thermal Insulation & Foaming html Copy Edit
PU Foaming
- Low-Pressure PU Foaming
- High-Pressure PU Foaming
- In-Cavity Foaming
- Foam Density Control
Insulation Panel Assembly
- Vacuum Insulated Panels
- EPS Sheet Fitting
- PU Slab Placement
- Reflective Film Lamination
Foam Mold Fixtures
- Cabinet Moulds
- Door Foaming Moulds
- Rotating Fixtures
- Heated Steel Plates
Foaming Process Aids
- PU Mixing Heads
- Flushing & Purging Systems
- Cycle Time Control
- Foam Overflow Traps
Final Assembly & Packaging
Mechanical Assembly
- Snap Fit Assembly
- Screw Fastening
- Riveting
- Clip Mounting
Electrical Assembly
- Connector Crimping
- Wire Routing
- Terminal Fixing
- Harness Mounting
Packaging & Kitting
- Carton Assembly
- Thermocol / Foam Inserts
- Accessory Pouch Insertion
- Instruction Leaflet Insertion
Testing & Labeling
- Leak Testing
- Electrical Function Test
- Barcode & Serial Tagging
- Final Quality Stamp
Advanced Data Capture Hardware
For unprecedented speed, scale & Precision
ASI has developed custom hardware systems to accelerate and standardize data capture during teardown. These tools integrate directly with xcPEP and enable fast extraction of both physical and electronic parameters with minimal manual input. By digitizing key steps such as PCB component identification, bounding box measurement, and projected area capture, the hardware reduces lead times and ensures consistent, reviewable inputs for cost model generation. This setup is built to support high volume costing programs where speed, repeatability, and data reliability are critical.
AI-Based Component Identification for PCBs
In home appliances, PCBs are used across inverter boards, control modules, displays, and power supply units. Identifying each component manually is slow and error-prone, especially when dealing with large teardown batches.
ASI Engineering uses an AI-based imaging setup to scan each PCB and automatically identify mounted components such as ICs, capacitors, resistors, and connectors. The data is matched against xcPROC to populate fields like part name, value, and manufacturer. The BoM is then displayed inside xcPEP for review and costing.
Bounding Box Dimension Capture for Large Parts
Dimensional inputs like length, width, and height are essential for costing plastic, sheet metal, and structural parts in appliances. Manual measurement using calipers or tapes is often slow and inconsistent, especially for irregular or bulky parts.
ASI Engineering uses a laser-based system to measure all three dimensions without physical contact. The part is placed inside a calibrated enclosure, and the bounding box values are recorded and transferred into xcPEP for use in process and packaging cost calculations.
Projected Area Capture System
Projected area is a key input for calculating tonnage in moulding and sheet forming. It also affects material usage and surface finishing in panels, trays, and structural covers.
ASI Engineering uses a calibrated vision system to scan the part, detect the outer profile, and calculate the 2D area in real units. This is especially useful for high-volume costing of repeat parts like washing machine covers, microwave panels, or refrigerator liners.
Outcomes of
Home Appliance Should Costing
Should costing by ASI Engineering helps appliance programs move beyond assumptions and supplier-driven pricing. Using real manufacturing steps and verified input data, every part is analysed with clarity and precision.
Below are some of the key outcome's teams see when structured should costing is applied across their product platforms.
Transparent Cost Visibility
ASI Engineering provides part-wise cost breakdowns built from real manufacturing steps, not averages or estimates. Every material, process, and operation is traceable—giving teams full visibility into how cost is created across plastics, metals, and electronics.
Faster Alignment Across Teams
With structured costing in xcPEP, sourcing, engineering, and finance teams work from the same set of data. This reduces back-and-forth during reviews and helps cross-functional teams converge on cost targets more quickly.
Baseline for Cost Reduction and Localisation
Structured costing provides a clean reference for identifying high-cost parts, comparing alternative builds, or evaluating regional production strategies. This supports ongoing cost-down initiatives without compromising function or quality.
Stronger Supplier Negotiations
With part-wise costing and process-level transparency, commercial teams can enter supplier discussions with confidence. The data acts as a neutral baseline to support renegotiations, clarify expectations, and reduce pricing ambiguity.
Make-vs-Buy Decisions
Structured cost data enables internal teams to evaluate whether a component should be sourced externally or produced in-house. With process-level granularity, teams can model both options and compare them directly.
How are we different?
Most costing tools stop at BOM level insights or depend on external assumptions. ASI offers something stronger. xcPEP is a structured cost engineering platform built on real manufacturing logic, not estimates or rollups. Should costing is carried out by ASI Engineering with unmatched speed, precision, and accuracy. The team works directly on appliance components using real process steps and verified input data.
Together, xcPEP and ASI Engineering offer the most complete solution for accurate and defensible should costing, delivering both the technology and the expertise needed to drive real impact.
Column Title
SpreadSheets
BOM based tools
Management Consultants
xcPEP + ASI Engineering
Real-world process accuracy
Verified input data
High-speed performance
Shorter learning curve
Comprehensive process coverage
Scalable engineering support
Lower cost of ownership
API-based integration
Use Cases of xcPEP in Home Appliances
Used by sourcing, engineering, and product cost teams—from new platform costing to supplier negotiations.
xcPEP is widely used by appliance OEMs and suppliers to support structured should costing across a wide range of systems—from motors and harnesses to tubs, control boards, foamed panels, and subassemblies. It supports everything from early design analysis and quote validation to benchmarking and ongoing cost optimization.
Below are few use cases where xcPEP delivers impact in home appliance programs.
In-House Cost Lab Setup
xcPEP was deployed to establish a cost lab for a global washing machine manufacturer, following a Build–Operate–Transfer model. ASI Engineering configured the platform, migrated legacy costing data, and aligned xcPEP with the customer’s BOM structure and appliance hierarchy. Joint costing projects were executed to build initial models and train the internal team. Once confident, the team fully took over operations. Today, they run their own cost lab on xcPEP, with ASI providing database updates and support as needed.
Should Costing for New Part Development
xcPEP was deployed for a global kitchen appliance manufacturer to support should costing during early part development. ASI Engineering worked with the design and sourcing teams to cost key components such as motor housings, heating coils, and PCB assemblies before supplier quotes were received.
Cost estimates were built using real manufacturing steps and xcPROC inputs for region specific machine, labour, and material rates. This helped define cost targets early and reduced dependency on external benchmarks during sourcing.
Fact Packs for Supplier Negotiations
xcPEP was deployed for an air conditioner manufacturer to support cost-backed supplier negotiations. ASI Engineering created detailed cost references for components such as brackets, control panels, harnesses, and display systems. Each part was modelled based on real manufacturing operations like injection moulding, spot welding, and SMT assembly.
The outputs were compiled into structured negotiation packs, helping teams validate supplier quotes, identify cost gaps, and negotiate from a clear position of process-level understanding.
Competitor Cost Benchmarking
xcPEP was used to benchmark the cost of a client’s refrigerator against a competing brand. ASI Engineering conducted a structured teardown of both models, capturing detailed inputs on materials, assembly methods, and component choices. Each part was modelled using real manufacturing logic and costed using region-specific data from xcPROC.
The outcome was a side-by-side cost comparison at the part and system level, helping the client identify cost gaps, design inefficiencies, and opportunities for sourcing or value engineering improvement.
Set Up Your Own Should Costing Lab with xcPEP
Product Studies
Cost engineering projects executed internally by the ASI Engineering team.
This section highlights detailed should costing studies carried out by ASI Engineering across a range of home appliance platforms. Every teardown, part image, and cost breakdown presented here is based on ASI’s independent engineering work.
The focus is on building transparent, process-based cost models that reflect how each component is actually manufactured. Studies span systems such as washing machines, refrigerators, air conditioners, and kitchen appliances—demonstrating how clean input data and real manufacturing logic lead to accurate, defensible costing outcomes.