xcPEP Deployment
Handled end to end by ASI Engineering
We partner with your cost engineering, sourcing teams and other stakeholders to deliver a robust and effective should costing rollout.
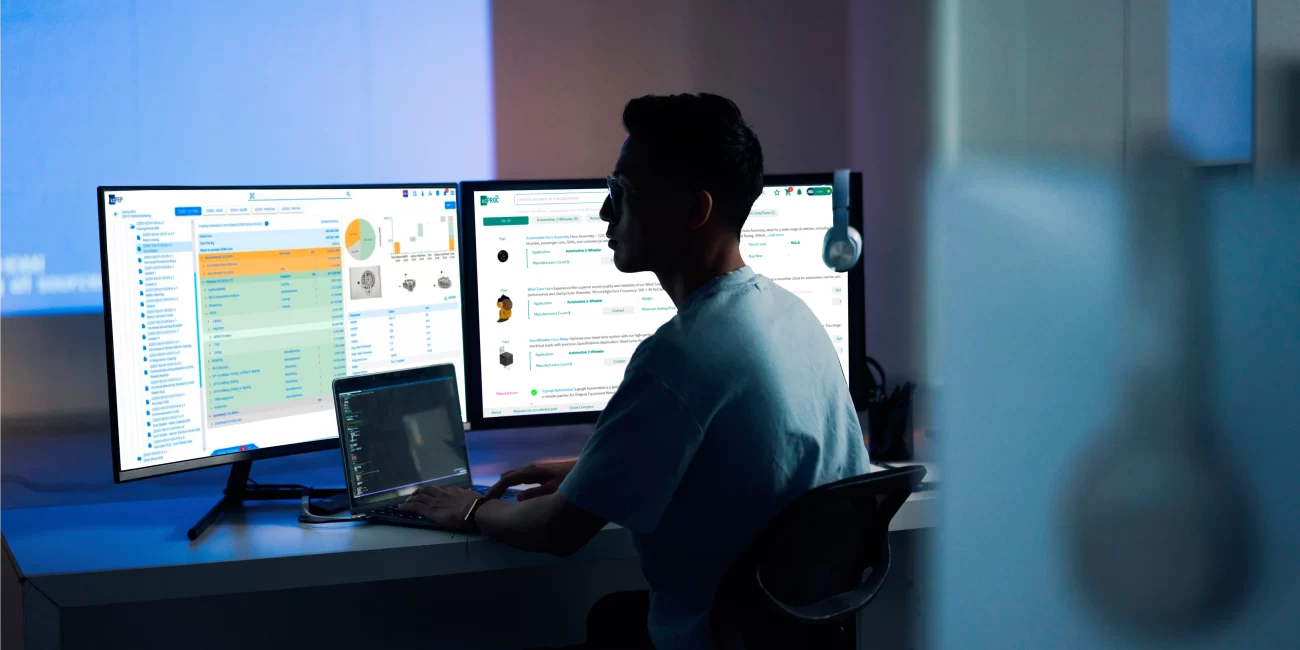
Requirement Mapping & Planning
Our approach begins with understanding your organization’s current costing maturity and aligning xcPEP’s capabilities to your goals.
Activities at this stage are:
Stakeholder workshops to define the business case for should costing.
Identification of pilot categories or commodity families.
Integration planning with existing PLM, ERP, and design workflows.
Definition of target outcomes.
Data Discovery, Cleansing & Migration
Effective should costing requires clean, structured, and traceable data. ASI Engineering supports every aspect of data readiness. This ensures a clean and scalable data foundation for should costing analytics.
Activities at this stage are:
Cleansing of BOMs, drawings, and cost records.
Mapping part attributes to xcPEP’s data model.
Migration of part master data, historical costs, and supplier inputs.
Upload and verification inside xcPEP.
BOM & Cost Model Configuration
Every manufacturer has a unique way of organizing products into product lines, each with its own BOM structure, grouping logic, and nomenclature. Additionally, variations in regions, production volumes, quality standards, and internal cost models require tailored adjustments.
ASI Engineering handles all of this during the configuration stage—ensuring xcPEP is fully aligned with each customer’s specific product architecture, operating norms, and cost modeling requirements.
Database Configuration
ASI Engineering creates and configures various types of database for effective use of xcPEP
Most manufacturers have a database of raw materials used in their built-to-print parts category. Since xcPEP covers all parts for costing, ASI Engineering works with customers in creating raw material database for built-to-spec and proprietary parts as well.
Every large manufacturing company has a diverse supply chain. ASI Engineering maps the regions, popular machines in each category being used in those specific regions and corresponding costs of purchase, operation, maintenance and power etc. This ensures xcPEP customers are always working with the most realistic input parameters for costing.
Large manufacturing companies operate across regions with varying labor dynamics. ASI Engineering captures region-wise labor classifications, standard job roles, prevailing wage rates, and associated overheads like statutory contributions, training, and shift differentials. This enables xcPEP users to cost with regionally accurate labor hour rates, ensuring estimates reflect real-world conditions.
Manufacturing companies often use a wide range of standard parts—such as resistors, capacitors, ICs, fasteners, bearings, seals, and bushings—within their products. ASI Engineering builds a customized database for each customer, mapping the exact standard parts involved in both in-house manufacturing and externally sourced assemblies.
In global supply chains, forex conversion and hedging plays a significant role. We map your global supply chain and create a database of relevant currencies so costing outputs are always aligned with real work scenario.
System Deployment & Integration Support
Whether you’re running SAP, Oracle, Teamcenter, or a custom ERP, our team can integrate xcPEP with your enterprise systems securely.
We support
Training
Our hands-on training programs empower cross-functional teams to become confident users of xcPEP and skilled practitioners of should costing. We provide tailored training and support for all stakeholders, aligned with their specific roles and use cases within xcPEP. Training can be delivered on-site, online, or in a hybrid format to suit customer needs.
Ongoing Support
We support your internal teams in an ongoing manner to ensure xcPEP is utilized in a manner most suitable to your business requirements. Towards this end we provide the following services: